
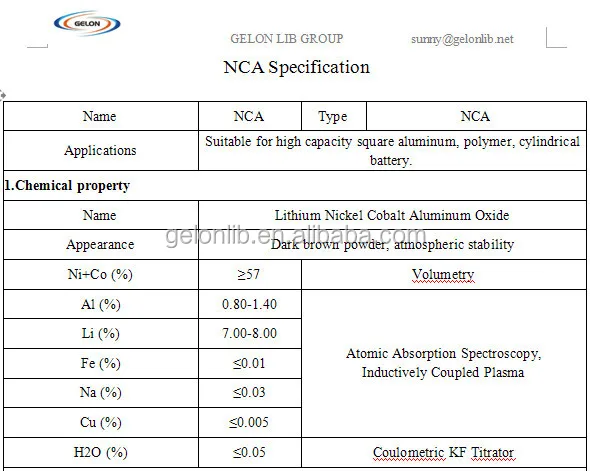
Results indicated a higher amount of mullite formation in porcelain bodies containing TiO 2. The overall degree of crystalline and amorphous phase content within the porcelain bodies was quantitatively determined using a Rietveld analysis. Porcelain rods were fired under industrial scheduling in a manufacturing kiln.
#NMC CATHODE SINTERIZING SERIES#
A series of alumina porcelain bodies containing increasing amounts of TiO 2 were prepared by extruding mixtures of raw materials and TiO 2. An interesting and innovative method is used to reflect the corrosion degree of the sample, and the reliability of this method is guaranteed by combining the loss rate of preparing the cathode material.Ībstract The effect of adding TiO 2 to standard alumina porcelain on its microstructure and flexural strength was investigated.To improve the corrosion resistance of mullite-cordierite material was realized by adding CAT as a third component ( one kind of solid waste from the production of ferrotitanium alloy), and it was useful to reuse CAT.Unlike the outdated mullite saggars that had been studied and published in other journals, the saggar studied in this paper was innovative and mature in use. This study investigated saggars in the market.Thus, the mullite-cordierite-CAT composite material is more suitable for the sintering of Li-ion battery cathode materials. Experimental results demonstrated that CAT could reinforce the consolidation of the matrix in the sintering process and effectively enhance the corrosion resistance of the mullite-cordierite composite material. Optimized crucible samples with various CAT contents were prepared and subjected to static corrosion resistance tests. To improve the corrosion resistance of mullite-cordierite saggar, calcium alumino-titanate (CAT) was introduced as the third component. LNO Li-ion battery NMC Ni-rich layered oxide calcination cathode heat-treatment.In this study, a post-mortem analysis of saggars after service was performed to analyze their internal structure and damage mechanisms. The importance of a careful selection of the heat treatment (calcination) temperature for each individual cathode material was emphasized. Despite their well-ordered structure, the materials calcined at higher temperatures were characterized by a stronger sintering effect, adverse particle growth, and higher Ni 2+/Li + cation mixing, thus deteriorating their electrochemical properties. The NMC-900 calcined at 900 ☌ and the LNO-700 calcined at 700 ☌ showed the most favorable electrochemical performances. With increasing nickel content, the optimal calcination temperature shifts towards lower temperatures.
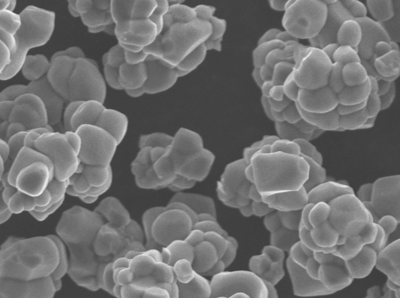
It was determined that the optimal calcination temperature is dependent on the chemical composition of the cathode materials. The correlation of the calcination temperature, structural properties and electrochemical performance of the studied Ni-rich layered cathode materials was thoroughly investigated and discussed. The samples obtained at different calcination temperatures (750-950 ☌ for the NMC622 and 650-850 ☌ for the LNO cathode materials) were characterized using nitrogen physisorption, PXRD, SEM and DLS methods. Ni-rich layered oxides, i.e., LiNi 0.6Mn 0.2Co 0.2O 2 (NMC622) and LiNiO 2 (LNO), were prepared using the two-step calcination procedure.
